「”VA活動”や”VE活動”って、どう違うの?」
「”VE活動”は設計から、”VA活動”は量産で行う売価低減でしょ?」
と、いうように”VA活動”や”VE活動”は会社での改善活動や顧客からの要求で行われることがあるので、単純にコストカット、売価低減の活動を指すと勘違いをされている方もいらっしゃいます。
そのため、値段を下げることにばかり注意が行ってしまったり、参加者の理解度の違いによって目指す先が違うために活動自体がふわふわとして、結局何をやってたんだっけ?
と、いうようなことになりかねませんので、きちんとVA活動とVE活動の違いや目的を参加者全員が理解しておく必要があります。
“VA活動”と”VE活動”の定義
VA(Value Analysis – 価値分析):量産製品に対して、バリューチェーン全体から原価低減を行う活動
VE(Value Engineering – 価値工学):製品開発(設計検討)段階から、価値の最大化を考える活動
価値(Value):製品やサービスの価値は、それが果たすべき機能を、そのためにかけるコストで除した関係にある
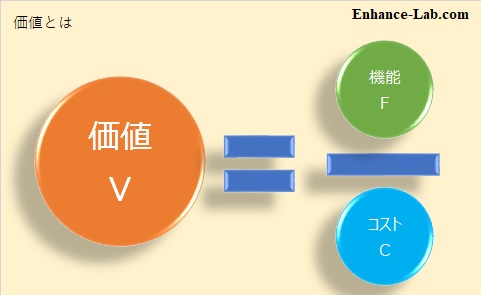
と、いうことで、VAはすでに量産している製品を対象としているため、製品に要求する機能はそのまま維持されなくてはなりません。
左辺にある価値Vを向上させるのが目的ですが、右辺の分子である機能Fを変えずに行うべき活動となりますので、分母のコストCを削減することになります。
そのため、活動としては原価低減(コスト低減)が主となります。
VEでは、開発・設計の段階から価値の最大化を目的としているため、原価低減(コスト低減)だけではなく、機能の向上も含めた形で検討することで、価値の向上を考える活動になります。
VA/VE活動における”機能F”と”費用C”について
- 顧客要求に沿うものが、”機能F”に含まれます。(例えば、品質や性能、安全性、納期、環境への配慮など)
- 顧客要求への影響がなく、費用につながるものが、”コストC”に含まれます。(例えば、生産性や原価など)
- これらの項目は、生産管理をする上で重要な7項目(PQCDSME)を基準にして見ることが大切です。
PQCDSMEとは?
一昔前では、「QCDで報告するように!」などと言われていましたが、今では労働者環境や社会とのつながりなどが会社に与える影響も大きなものへと変わってきています。
このようなマーケティングと強い関係性から、生産管理をする上で重要な7項目として、このPQCDSMEを基準として考えることが求められています。
例えば、”ただ作れば売れた時代”には、生産性だけを追求していましたが、”消費者が裕福になり、消費者が商品やサービスを選択する時代”となると、品質やコスト、納期などへの取り組みが重要となりました。
そして、”現在”では安全や環境、労働者のモラールへの関心も高まっており、これらが会社の評価に対するとても重要な要素となっています。
Productivity(生産性)目線での改善
労働生産性の向上、設備可動率や生産可動率の向上 → 生産しやすい工程など
いわゆるインプット(投資)に対するアウトプット(リターン)の割合です。
- サイクルタイム短縮のために、材料の見直しや生産条件の変更の検討
- 可動率向上のために、段替え効率の改善や不良率の低減
- 生産性を悪化させる形状の見直し(機能には影響がないことが前提)
Quality(品質・性能)目線での改善
不良率の低減、検出率向上、機能充足度や満足度の向上 → 顧客要求の満足など
- 標準作業の見直しによる不良率の低減
- 検査工程、治工具設計の見直しによる検出率の向上
Cost(費用・経済性)目線での改善
原材料費や労務費、経費の削減 → 原価低減など
- 買い方改善や代替品への置き換えによる原材料費の低減
- 省人化や標準化による労務費低減
Delivery(納期・生産量)目線での改善
ジャストインタイム生産、輸送効率向上、スペースの有効活用 → 生産システムや物流など
- 発注管理や生産管理、在庫管理による生産性の安定や在庫スペースの縮小
- 梱包箱や収納方法の変更による積載効率の向上
Safety(安全性)目線での改善
使用者、利用者だけでなく、作業者の安全性も含めた安全の向上 → 労災やPL法、企業の信頼など
- 定期的な検査による法規制遵守
- PL法などの基礎知識の習得、社内教育の実施
- 不安全行動の抑制につながるような設備、作業のチェックや教育訓練
Morale(モラール)目線での改善
職務満足度の向上、職場環境や帰属意識 → 働きやすい環境づくりなど
- 作業者の負担になるような作業や、材料を取り除くような見直し
- 現場の困りごとを吸い上げるなど、モチベーション向上につながる施策の実施
Environment(環境)目線での改善
廃棄物の処理、環境負荷物質への対応 → 法規対応、周辺環境への配慮など
- リサイクル法、化審法の他、海外の環境規制の基礎知識習得、社内教育の実施
“VA活動”における注意点
定義に示されているように、VAでは機能Fを維持しなければなりません。
そのため、下記のような活動を行うことはVAとしての改善にはならないため、注意が必要です。
事例1 労務費削減のため、品質検査員を配置することを止める
品質検査員を工程の最後に置いていましたが、省人化とサイクルタイム削減のために検査員を置くことを止めました。
もし、品質検査員がいなくても、顧客要求品質を満足できるような工程が作られていた場合には、VAとなり得ますが、そうではない場合には、品質Qの低下は機能Fの低下となりますのでVAとはなりません。
事例2 日本材を使うことになっていたが、中国材に切り替え
こちらも切り替えた中国材が全く同等性能であり、評価などを行った結果問題ないことが証明されており、コストが抑えられるのであればVAとなります。
しかし、きちんと確認がされておらず、性能が劣ったり、環境に影響のある規制物質が含有していた場合などは機能の低下となりますのでVAとはなりません。
さらに、過去にもこのような事例で環境規制物質が含有していることが後に分かり、切り替え当時までさかのぼって商品の回収、交換を行うことで数百億という損害を受けた企業もあります。
海外材料への変更は法規制での基準値が違う場合もありますので、注意が必要です。
特に、このような問題が起きると、黙って他にも悪いことをしているだろうということで、信用を失うことにもなりますので、「面倒だから」、「どうせ分からないから」ということではいけません。
事例3 設備が動いているときでも作業者が作業できるように安全装置を切る
サイクルタイムの向上を図るためや、設備を止めると再起動に時間がかかるなどがあるため、光電管スイッチを切って作業させたり、設備を止めずに設備内に入らせる、もしくは定常的に動いている設備を触ることを良しとしている現場ではいけません。
作業者の安全は、顧客要求として求められるものではないため、機能Fには含まれませんので、ここが低下しても機能Fは低下しません。
ですが、事故が起きれば損害賠償や生産停止、信用を失うといった大きなリスクを負うことになります。
ちょっとした目先のタクト改善のために、経営に大打撃を与えかねないリスクを背負うことは、長期的な視点で見た時にコストCの低減とはなりませんので、そもそもコストの改善にはつながりません。
“VE活動”の基本原則
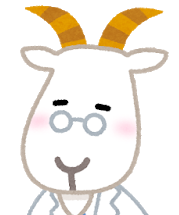
ここからは、”VE活動”に関する内容になります。
VEについては、”公益社団法人 日本バリューエンジニアリング協会”が
基本原則や実施手順を示しています。
協会の示す内容を参考にしながら、実務に沿った形で整理しましょう。
VEの基本原則とは、価値ある製品やサービスを追求する活動を、正しい方向に誘導するための行動指針にあたるものです。
使用者優先の原則:顧客要求から外れたものにならないように改善の照準を合わせる
機能本位の原則:Why-How-Whatの視点で疑問を大事にし、機能本位で考えること
想像による変更の原則:現状や固定観念にとらわれず、新しいアイデアを批判しないこと
チーム・デザインの原則:各分野の専門家によるCFT(クロスファンクショナルチーム)を組織すること
価値向上の原則:V=F/Cの概念式に基づいて、価値の向上を図ること
VA/VE活動を行うにあたって、会社として取り組もうとしてもVA/VEのやり方や内容を理解させられていないと帳面消しのような活動になります。すると、設計者がひとりで行っているなんてことも。
「顧客要求に外れない」、「新しいアイデアの創出」などは一人の視点では難しいものですので、CFTメンバーで検討するとなっています。これはFMEAにも通じるものです。設計部が設計をするものと考えがちですが、設計部は設計を主幹しますが、チームみんなで取り組むことでより良い製品が作れることが意識できると良いですね。
“VE活動”の実施手順
VE活動により、効果的に問題解決するための基本ステップです。
1.機能定義 | VE対象の情報収集 | VEを行う製品やサービスの情報を 関係者で収集、共有していく |
機能の定義 | 名詞と動詞の二語を使って、 「~を~する」と簡潔に表現し、 VE対象の機能を抽出していく | |
機能の整理 | 抽出した機能を「目的→手段」の 関係で機能系統図を使って整理 | |
2.機能評価 | 機能別コスト分析 | 各機能の達成に費やされている コストを明確にしていく |
機能の評価 | 各機能に価値を持たせる上で 基準となるコストを設定する | |
対象分野の選定 | 改善を推進していく機能分野の 優先順位を決める | |
3.代替案作成 | アイデア構想 | 機能の整理で抽出した手段の 代替や新技術への置き換えなど アイデアを集める |
概略評価 | 技術面とコスト面から可能性を 確認し、どうしても実現しそうに ないアイデアのみ落とす | |
具体化 | 残ったアイデアを多角的な視点で 検討し、練り上げていく | |
詳細評価 | 採用を考えるアイデアの安全性や 機能性、経済性などを最終評価 |
具体的な例
それでは、オーブントースターで簡単に流れを追ってみます。
VE対象の情報収集では、これからVEの検討を行うオーブントースターの製品、品番、名称、売価や原価、どこの工場で製造されているかなどの情報を活動メンバー間で共有することから始めます。
機能の定義+機能の整理
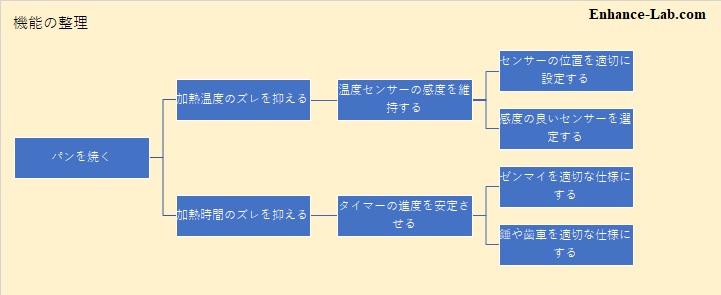
「~を~する」の形でいくつもの機能を抽出し、それぞれの機能について機能系統図を用いて機能の掘り下げを行っていきます。
ここでは、”パンを焼く”という機能を抽出し、それに対しての掘り下げをしています。
実際には、最後のセンサーの位置や仕様、ゼンマイの仕様はもっと細かく、太さや使用領域などを特定していくわけですが、今回は流れを追うだけなので簡単に”適切な仕様にする”とひとくくりにしています。
この時の注意点として、
- 1つのマスには、”機能の抽出”に従い「~を~する」の形で記入する
- 左側のマスが”目的”→右側のマスが”手段”とつながるような形で掘り下げる
- 1つのマスに2つ以上の手段を記入しない
- 具体的に記入する
- 自分たちの力が及ぶ範囲で掘り下げる
以前の記事で、トヨタ流のなぜなぜ分析を基にした、要因分析で行った手法とも似ていますよね?なぜなぜ分析では「左側が問題」で「右側がその要因」、VEの場合は「左側が目的」で「右側が手段」です。
QCサークルやJISQ9024など、一般的には複雑に絡み合った問題の要因分析では連関図法を用いるようにまとめられているのですが、なぜなぜ分析(要因分析の手法)では系統図法を使用します。
色々な手法を知っているというのも武器ですが、ひとつの手法を深く掘り下げるというのも強力な武器となりますので、私は系統図法によるVE解析や要因分析を推奨しています。
なぜなぜ分析の記事はこちら⇩
機能別コスト分析
話を戻しまして、細かな機能を抽出したら、それぞれの機能の価値に対してコスト分析をしていきます。
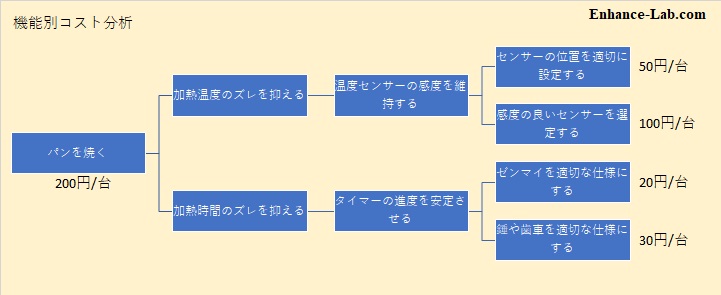
コストで評価する理由は、判断の基準を定量的に測れるようにするためです。
例えば、”センサーの位置を適切に設定する”ために少し加工が必要となり、それに50円のコストがかかるとすると、その機能には50円の価値があるというような具合で、その機能の有無によって、どれだけのコストがかかっているかを整理していきます。
機能の評価
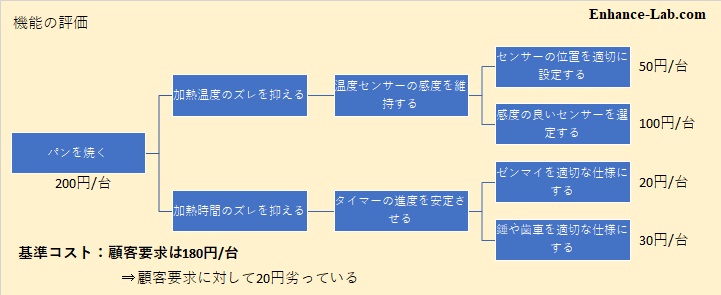
そして、他社比較や顧客要望を参考にして、それぞれの機能に求められる基準コストを設定し、自社製品の分析コストと比較を行うことで、各機能に費やしているコストの評価を進めていきます。
この場合、パンを焼くという機能に対して、顧客は1台のオーブントースターに180円のコストで作って欲しいと要望されていますが、実際には200円かかってしまっており、顧客要望に対して20円未達の状態だと評価をしました。
対象分野の選定
パンを焼くという機能については、20円劣っている状態だったわけですが、他の機能はどのような結果だったかを横並びで見ていきます。
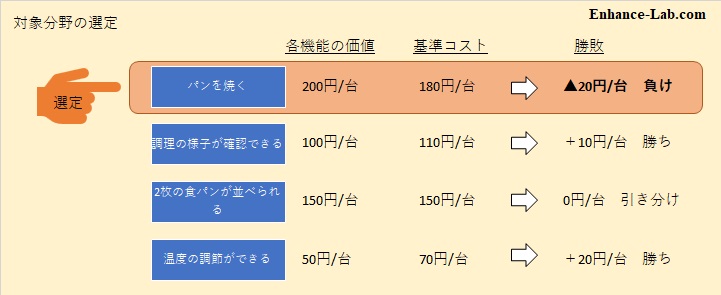
すると、他の機能は顧客要望を達成しており、競争力も十分にあることが評価されました。
ですから、VEとして取り組むべきは、要望未達のパンを焼くという機能が選定されます。
このような流れで活動のポイントを絞っていきますが、他社が出来ているのに自社が出来ていないことであったり、顧客要望を満足していない部分への改善とすることが望ましいです。
代替案の作成
このように、適切な活動ポイントを絞り込むことで、経営資源を投資するにあたってのムダを削減することにつながります。
そして、ここから問題や課題といった現状とのギャップを埋める活動の計画を立て、PDCAサイクルを回しながら改善活動をすすめるというステージに入っていきます。
PDCAサイクルの詳細は下の記事を参考にしてください。⇩
“VE活動”で価値を上げる方法
VE活動で考える、製品やサービスの価値Vは、それが果たすべき機能FをそのためにかけるコストCで除した関係で表されます。
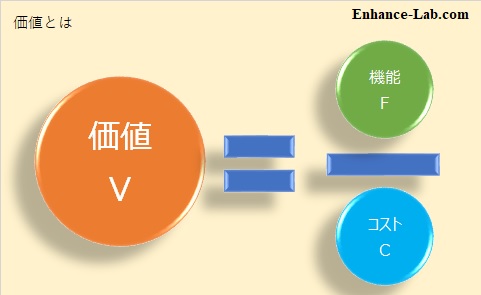
ですから、この左辺の価値Vを上げるためには
①機能を維持⇨して、コストを低減⇩する
②機能を向上⇧して、コストを維持⇨する
③機能を向上⇧して、コストを低減⇩する
④コストは増加⇧するが、それ以上に機能を向上⇧⇧する
の4つの方法が考えられます。
このとき、「機能は低下⇩するが、それ以上にコストが低減⇩⇩する」と、いうパターンでも左辺の価値Vは増加しますが、機能が低下することからコストカットやダウンサイジングなどの別の製品やサービスの開発と定義されるために、ここには含みません。
そして、VE活動で考えるコストは、”製品の開発”~”廃棄”までの製品の「総ライフサイクルコスト」で試算することが必要とされています。
まとめ
VAとVEの活動の定義や流れを整理してきましたが、VAとVEの考え方は少しずつ違いがあり、VA/VE活動などと一緒に呼ぶことも多いかと思いますが、活動自体は一緒にしてしまってはいけません。
VAで抽出したアイデアをVEに活かす、VEでの活動成果をVAに活かすというような、連携をさせる意味合いではとても有効です。
しかし、VA活動での対策を考える場面でVEの考え方をしてしまってはいけませんし、VE活動の中でVA手法だけでイメージしていてはアイデアが広がりません。
きちんとメンバー全員が活動の目的を理解し、同じ方向を向いて進めるためにも、VAとVEの違いを理解し、基本的な流れを頭の中にイメージとして持っておくことが必要になります。