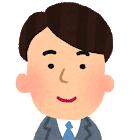
不良品がお客さんに流出したので、ダブルチェック検査で
対策をしたのですが、問題が再発してしまいました。
今度はトリプルチェックで検査しますと報告が上がってきました。
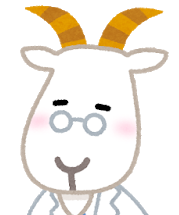
安易に最終検査員を増やしても不良品の流出は止まりません。
さらに、労務費の上昇で利益も圧迫しますし良いことなしです。
部下からそのような報告書が上がってきたら一緒に要因分析!
OJT教育することで部下のスキルアップにもつながりますよ。
不良品をお客さんに納めてしまって対策を求められた際、ついつい人をかけて検査すれば大丈夫!と、してしまいがちです。なぜなら、対策が簡単だから。問題の要因が潰せていないため、対策ではなく処置でしかありません。
これでは再発して当然です。
今回は、再発させない対策の取り方について整理をしていきましょう。
ダブルチェック検査をするデメリット
設備や治具を改造して対策しようと思うと時間も費用もかかるから「人」で対策。
例えば、1ヵ月間に2人目の検査員が不良品を発見することがなかったら、「きっと不良品は流れない工程になったのだろう」と判断して、ダブルチェック検査をやめられる。きっとまだ工程が熟成されていないから、慣れればきっと不良品はでないだろうからダブルチェック検査で対応しよう。
そんな思いでダブルチェック検査を対策としていないでしょうか?
こういう場合、必ず問題は再発します!
そして、ダブルチェック検査をしている最中に流出すればトリプルチェック検査をし、ダブルチェック検査をやめたあとに流出すれば、なぜダブルチェック検査を対策としたのにやめたのかと責められ、今後ダブルチェック検査が常態化。今後の生産品でも同じ対応を取らされることにつながります。
これにより発生するデメリットについて、簡単に整理します。
要求品質の上昇
不良品が納入されたお客さんとしては、「この会社の納入品には、また不良品が混じっているかもしれない」と考えます。そのお客さんも受け取った部品を使って製品を作っている場合、自分たちのお客さんに不良品を納めることにもなりかねませんから、神経質になります。
そのため、受入検査で不良品が入ってくるのを止める必要があるわけですから、不良品が流れてきたら今度からもっと気を付けて見ておこうとなります。
これまで、サラッと見ていた納入品チェックを別の角度からも見ておこうとなるかもしれません。グレー判定の製品がくれば、これまでOKと判断されていたとしても、じっくりと見られることでNGと判定されるかもしれません。
一度グレー判定品がNGとなれば、今後はそのグレー判定品が良品限度として扱われてしまいますから、品質要求はどんどん高くなっていきます。
人の目はとても曖昧です。
良いと思っていれば良く見えますし、疑って見れば悪く見えるものです。
コストアップ
品質要求が高くなれば、これまで良品として納められていた製品も不良品となってしまうわけですから良品率は下がります。良品率が下がれば製造原価はあがります。当然、ダブルチェック検査をするためには労務費もかかります。
例えば、1個あたり1,000円で売っています。良品率90%のときに、材料費が500円、労務費が50円、経費や償却費を差し引いて、粗利が350円となる製品を作っているとしましょう。
品質要求が上がったことで良品率が90%だったものが80%となり、さらにダブルチェック検査で作業者を1名追加した場合の影響を見てみます。
良品率が90%であれば、10個生産すると9個が良品として納入できていましたが、良品率が80%となると、10個生産して8個しか良品として納入できません。そのため、余分に作らなければならなくなりますので、原価が増加します。
良品率90% | 良品率80% | さらにW検査 | |
売価 | 1,000円 | 1,000円 | 1,000円 |
材料費 | 500円 | 562.5円 | 562.5円 |
労務費 | 50円 | 56.25円 | 112.5円 |
経費 | 50円 | 56.25円 | 56.25円 |
償却費 | 50円 | 56.25円 | 56.25円 |
粗利 | 350円 | 268.75円 | 212.5円 |
1ヵ月あたり10,000個を製造していた場合どうでしょうか?
月に粗利益が1,375,000円も下がってしまいます。
作業者の不満
こういった製品が増えていけば、当然企業としては費用の削減を行う必要が出てきます。そのような状況で従業員の給与を上げることは難しくなります。
次の新製品では、競合との受注争いをしようにも同価格であれば品質の高い方が選ばれますから、価格を落として受注を獲得していくことにもなるでしょう。そうすれば更に利益は減っていきます。利益が減れば従業員の給与は減っていきます。福利厚生も削られるでしょう。
すると当然、従業員は不満ですから、転職を考える方も増えていくでしょう。
生産品質の低下
人が辞めてしまうということは、教育して熟練度の上がった作業者が辞めてしまうということ。新たな教育をしていくにも時間もないでしょうから不良品はさらに増えてしまいます。また、検査員のレベルも下がってしまい、また不良品が流出しやすくなります。
今はSNSなどの拡大もあり、口コミなどのパブリシティの影響を大きく受ける世の中です。
転職サイトやオンライン上での低評価は、新たな従業員の獲得が難しく、優秀な人材が集まらなくなります。「企業は人なり」と言うように、重要な経営資源であるヒトを失うことは経営を維持していく上で大きな打撃となります。
負のスパイラルへ
「品質低下は、信用を失い、利益を失う」そして、利益を失った企業ではさらに品質低下が起きやすいので、どんどん企業価値は低下していくことになってしまいます。
対策の立て方
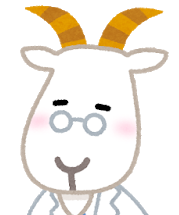
問題が起きたら「要因分析」!
特に発生原因を突き止めることが重要です。
当然ですが、発生原因が解決すれば問題は発生しません。
問題の要因を特定
問題の要因分析といえば、なぜなぜ分析です。
発生した問題につながる要因を掘り下げていき、真の要因を明らかにします。
要因の発生箇所を特定
要因を特定したら、その要因を取り除きます。
例えば、今回発生した問題を「間違った部品が付いていた」としましょう。
要因分析をしていき、真因が「他の製品で使う部品も隣に置いてあった」とすれば、使う部品以外は生産ラインに持ち込まないようにすることで対策ができます。
当然ですが、間違った部品が手の届く範囲にないのですから、間違った部品を取り付けてしまうことはありません。
発生原因の対策ができない場合
ですが、A製品→B製品→C製品→A製品…と、いう具合に連続して違う部品を取り付けなければならない工程もあり、A製品の部品もB製品の部品も手の届く範囲に置いておく必要があるときには、上記の対策を取ることができません。
この場合には、発生原因の対策ではなく、流出原因の対策を取ることで防ぎます。
例えば、「部品組み付け後にカメラチェックで正しい部品出ない場合には製品をロックする」というように、間違った製品を次工程に製品を流させない仕組みが流出原因の対策になります。
まとめ
不良品の流出といった問題の対策では、安易にダブルチェック検査を対策としてはいけません。コストアップや品質要求のアップ、工程が増えることでのリードタイム増加といった、QCDすべてで負担になります。
まずは、きちんと問題の要因分析を行い、発生原因を特定して対策すること。対策できない場合には、流出原因を特定して対策すること。この流れが大切です。
また、こういった量産体制での問題は、開発段階へのフィードバックもとても大切です。
「製品設計段階でA製品の部品はB製品には組み付かないようにする」、「工程設計段階で適切な部品以外が取り出せないような仕組みをつくる」といったように、FMEAなどを行う中で対策が先行して行えるだけでなく、多くの製品への横展開が可能となります。